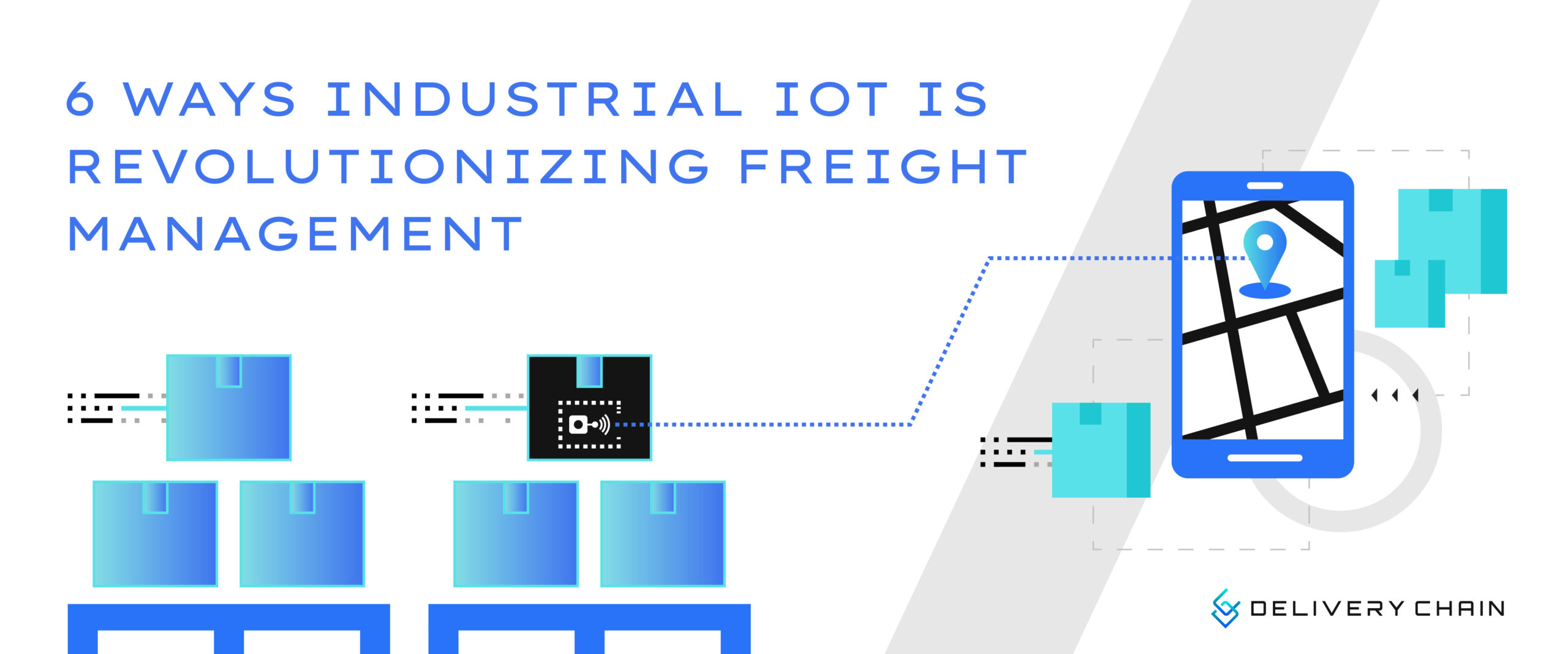
The Internet of Things has started to permeate all aspects of our lives, whether we’re telling Alexa to turn up the thermostat or using a Fitbit to track our steps. So, it’s only natural that the industrial IoT is thriving, too — helping organizations identify new efficiencies and opportunities than can change the way we do business. In fact, sensor trackers that deliver pallet-level intelligence™ instantly are already transforming the freight management systems industry.
The problem these sensor trackers solve for Logistics Service Providers (LSPs), shippers, and cargo owners is deceptively simple: more often than not, if someone were to ask if you know where your freight is, you’d probably have to answer “no.” In order to get some approximation of that answer, you might need to make a few calls or check for the limited information an electronic logging device (ELD) might provide.
But shippers also face additional challenges. Managing the day-to-day documentation and paperwork can be a lot to juggle — and even more so if your freight is damaged. Filing a claim can be a lengthy and uncertain process if you don’t really know what caused the damage. Long story short, there are a lot of scenarios in which current transportation management systems and warehouse management systems fall short — and where industrial IoT can deliver game-changing solutions.
Let’s take a look at 6 ways that industrial IoT can empower your organization to save time and money, and make the most of your freight management systems.
1. Know where your freight is at all times
In the pre-IoT days of shipping, you had several options if you wanted to know where your freight was:
- You could call the dispatcher or the driver of the tractor-trailer hauling your freight — that is, if your shipment is on a tractor-trailer, and you know which truck it’s on.
- You could check in on real-time ELD data — but this can be difficult with Less-Than-Truckload (LTL) shipment, which change vehicles frequently, or if they decide to rail your load.
- You could call the customer service representative with your freight management systems partner and rely on their word of mouth, but that’s ultimately not the most reliable method for tracking.
The problem with all of these options is that they take time out of your day — and time is money! What’s more, they might not provide truly verifiable insights into where your freight is right now.
All of this doesn’t even take into account that intermodal and international shipments present another unique set of challenges. An ELD won’t do you much good when your cargo is on a train.
The industrial IoT is changing all of this. A sensor tracker is placed with your pallet, not with the truck or the carrier. That means it provides you with data 24/7 — data that’s personalized to your particular freight. Check in anytime and as often as you want — you’ll always know where your freight is.
2. Say goodbye to check calls
When you’ve got round-the-clock access to up-to-date data about the status of your shipment, there’s no longer the need for check calls. This is a huge advantage — and not just because it saves you time and effort.
The safety improvements are first and foremost. The more phone calls your driver receives, the less they’re able to concentrate on the road, and on their main job, which is reaching their final destination safely.
What’s more, these kinds of calls were only ever capable of delivering incomplete information. Sure, the driver could tell you how far they were from the next stop, and reassure you that the freight was fine. But how much does the driver really know when they’re in the tractor, and your cargo is in the trailer? What if excessive braking or that deep pothole they hit earlier damaged some of your freight? Or what if temperatures in the trailer are fluctuating unpredictably? The driver doesn’t have a clear picture of these challenges until long after they happen.
Check calls to distribution centers are similarly incomplete. And while your freight management systems partner should always provide a customer service representative who’s willing and eager to help, nothing can match round-the-clock insights.
3. Stop losses before they happen
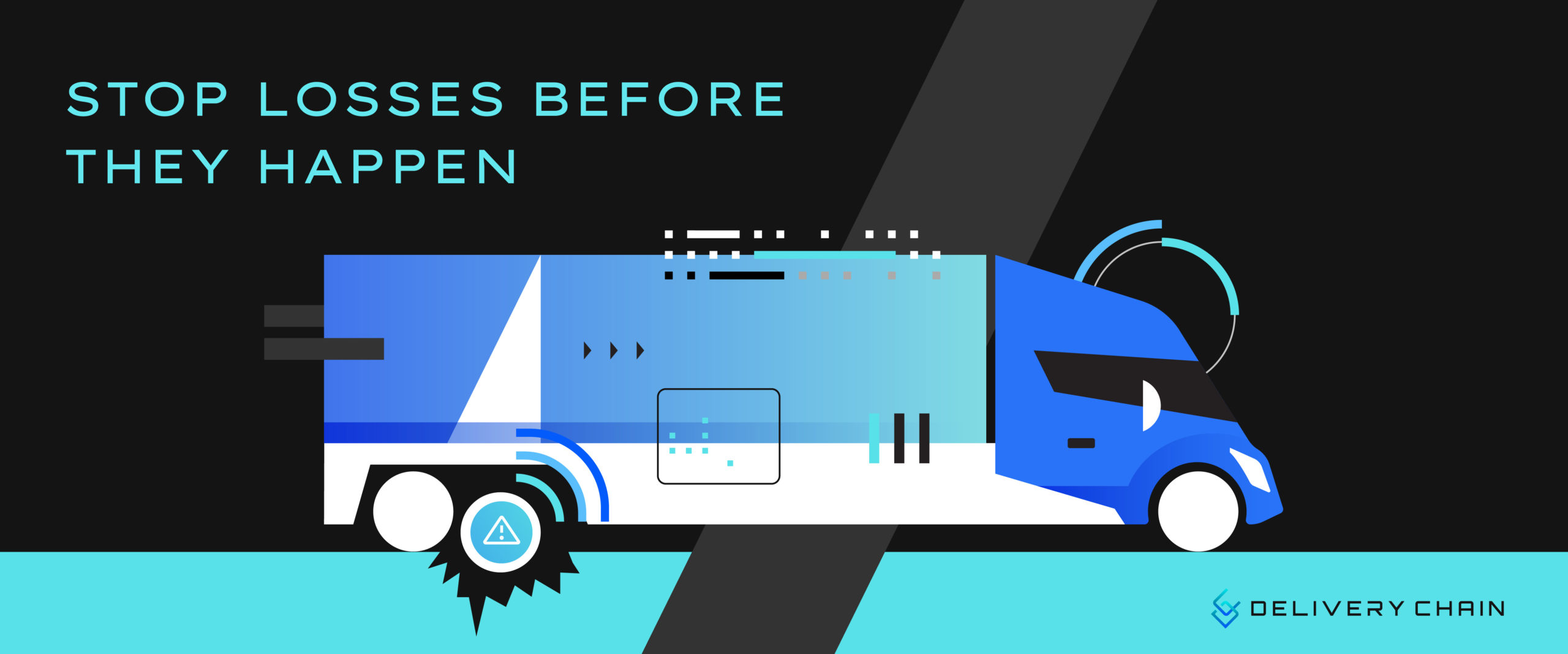
Every shipper needs to expect a certain amount of losses — it’s just a part of the business. But what if you could stop losses before they happen?
Industrial IoT doesn’t just provide a look at where your freight is, right now. The industry’s most advanced sensor trackers also include accelerometers and temperature monitoring. This means that if your freight experiences a sudden jolt or impact, or if temperature fluctuations are threatening the status of your reefer freight, you’ll be alerted immediately.
And these automatic alerts empower you to take action. Call your driver or customer service rep to get the issue addressed immediately, and they might be able to tie down loose cargo or readjust the temperature settings right then and there. The power to mitigate losses in these and other scenarios is one of the greatest advantages of industrial IoT.
4. File claims more easily
Even when losses do happen, industrial IoT empowers you to file better claims, more easily.
Before IoT, there was a lot of uncertainty around the claims-filing process. First of all, you need to determine who to file your claim with. That means determining when and where the damage occurred: During the loading process? On the road? And what caused the damage: improper dunnage or reckless driving? These things can sometimes be impossible to know for sure — that is, unless you’re working with a freight management systems partner that offers industrial IoT.
Because your sensor tracker is equipped with temperature sensors and an accelerometer, you’ll know exactly when and where G-force impact or other damage occurred. This allows you to answer a lot of those once-challenging questions easily, so you can file your claim faster and so that you’re more likely to be awarded the claim you deserve.
5. Manage documentation and paperwork effortlessly
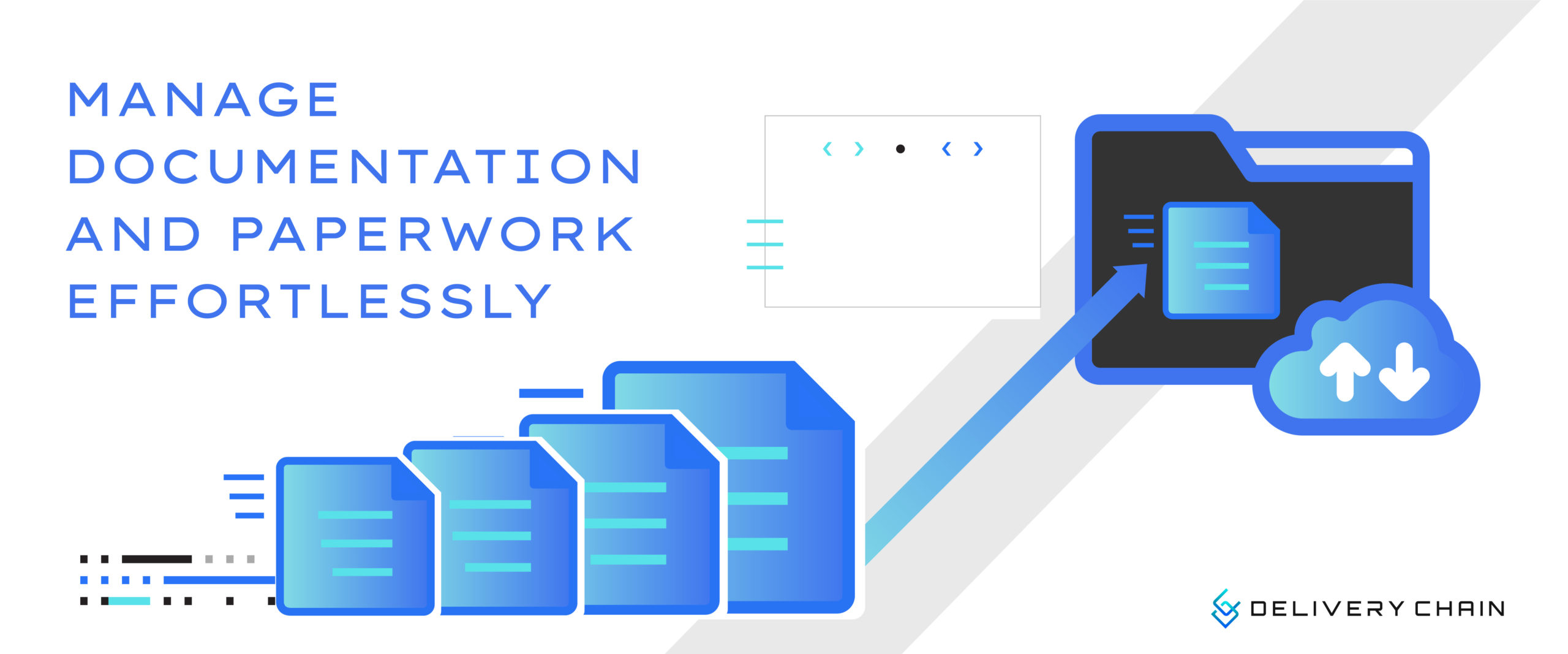
Juggling BOLs, weight certificates, Re-class invoices, and PODs can be one of the most overwhelming and time-consuming aspects of freight management. Not to mention, it’s not the most engaging part of your job.
Luckily, industrial IoT and leveraging our mobile solutions makes automatic document processing easy. That way, all the documentation that’s pertinent to your shipment can be delivered into your desired ecosystem without all the hassle — and without the papercuts.
6. Deliver better customer service
No business can be successful without happy customers. And industrial IoT empowers you to deliver better customer service.
One of the most important services you can deliver is real-time updates. But when you don’t know exactly where your shipment is, you can’t pass that information along to your customers. What’s more, when damage or delays occur, you want to let them know as soon as possible. That way, you can minimize the negative impact for all parties.
The geofencing technology built into sensor trackers ensures that notifications are sent to pertinent parties at key junctures. You can set important waypoints ahead of time — for instance, arrival at a particular distribution facility — so everyone involved will get an automatic notification when it’s arrived.
Industrial IoT: The future of freight management systems
No shipper, freight forwarder, or broker today can afford to live without industrial IoT. It gives you the competitive edge to build a more agile, data-driven, and service-oriented business. Ask your freight management systems partner what IoT solutions they can provide today.